304 vs 316 Grade Stainless Steel in Industrial Computing
Things Embedded specializes in providing stainless steel panel PCs and stainless steel displays for applied industrial applications that require either 304 of 316 grade stainless steel. These are two of the most common grades of stainless for industrial computing. There are many differences between the two despite them being indistinguishable in appearance. Manufacturing industrial monitors and panel PCs used in the food and beverage, pharmaceutical, and chemical industries with a stainless-steel chassis or front panel has many benefits. These specialist industries have stringent requirements to be highly water-resistant as cleaning, sterilisation and wipe-downs take place. With stringent requirements to stay clear of product contamination, these stainless steel HMIs are also exposed in the factory to industrial chemicals.
Manufacturing with stainless steel avoids risk of contamination, and providing it meets the right grade, meets the functional anti-corrosive requirements. This provides a longer life solution for the manufacturing needs while reducing the cost of ownership. There are five classes of stainless steel with the grades organized based on their crystalline structure. Both 304 grade stainless steel and 316 grade stainless steel are in the austenitic grade class with their structures making them non-magnetic and unable to be hardened by heat treatment.
304 & 316 Grade Stainless Steel Industrial Computing
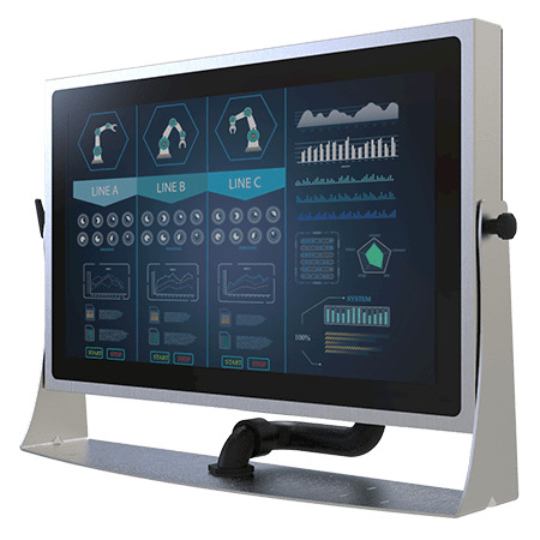
304 Grade & 316 Grade Stainless Steel Displays
What Are The Main Differences Between 304 & 316 Grade Stainless Steel?
Sighting visible differences between the two grades of stainless-steel sheet metal is near impossible to the naked eye, they are both grained and polished in the same way. Validation of the grade will take place by manufacturers to ensure the ordered grade is provided in the stainless steel monitors and stainless panel PCs.
All stainless steels contain a mix of iron and chromium at various levels. The exact mix with other additions is what creates the differences between the grades.
Stainless steels of the 304-grade, which is also known as “18/8 stainless steel,” contains 18% chromium and 8% nickel, whereas 316-grade stainless steel contains 16% chromium with 10% nickel and 2% molybdenum. The molybdenum is added to help resist corrosion to chlorides like sea water.
The benefits to 304 grade stainless steel are:
- Having a lower cost corrosion resistant option
- No limitations to fabrication
- Resistant to oxidation
- UL NEMA 4X Rated and Certified
The benefits to 316 grade stainless steel are:
- Superior corrosion resistance
- Can be used in offshore, marine and washdown applications
- Has chlorine resistance
- UL NEMA 4X Rated and Certified
Which Grade Stainless Steel Is Best For My Industrial Application?
Grade 304 is the most popular ordered stainless steel around the world with it offering the standard corrosion resistance, strength, formability and with it being easy to maintain. Grade 316, second in the number of quantities sold, offers a superior corrosion resistance to chlorides and acids. This makes it suitable for marine environments with high levels of dissolved salts.
The characteristics of 316 grade stainless steel makes it popular for a wide range of environments and applications such as:
- Medical and pharmaceutical
- Foodservice, processing and preparation
- Brewing facilities
- Coastal environments and maritime applications
- Ares with high salt levels
- Environments with increased exposure to alkalis and acids
With the increased resistances of 316 stainless steel, you can clean it with stronger cleansers and detergents with little worry of damaging or altering the appearance of the stainless steel. Therefore, this makes 316 grade stainless steel the superior choice and ideal for environments with strict hygiene and cleanliness standards.
Although 304 stainless steel will be less costly and suitable for most industrial applications requiring rugged specifications, 316 stainless steel provides the extra resistance in some situations where it may be required, adding years to its lifespan. This can then lead to drastic long-term savings despite a larger original investment.
An Important Note On Avoiding Surface Corrosion
There is an important factor which can affect the final performance of any grade of stainless steel, even the best. If a lack of care is given when preparing, the surface can cause them to appear to be rusting.
Irons tools which are used on non-stainless grades of steel could infuse the surface of stainless steel if proper care is not taken. If contamination takes place between the surface of the stainless steel and iron then it will develop corrosion stains from iron oxide which will make even the best grades of stainless steel appear to look like they are corroding. The contamination isn’t visible to the naked eye and so it may take numerous weeks for the corrosion of the surface to appear.
Special care will be taken by the manufacturers of 304 and 316 stainless steels to ensure that tools and sanding belts used on the stainless steel are not used with any other metals.
Need Help Selecting a Stainless Steel HMI?
Tell us about your application and a member of our team will get right back to you.