All Things USB. Industrial USB Applications Since 1996
USB stands for Universal Serial Bus and is a standardized protocol which enables computers to power and communicate with peripheral devices. Since its introduction in 1996 it has replaced not only PS/2, serial and parallel ports with a more compact connector but now contends against alternate high-speed protocols such as Ethernet. Latest advancements allow a single port to not only communicate with a device such as an Industrial Type C USB Display but carry video input, power, and touch input.
A surge in popularity of USB in the embedded marketplace over the last decade can be attributed to the continued advancement in USB technology and complete automation of many industries. This surge in IoT Internet of Things applications requires more and more connected devices which can communicate over different protocols, sometimes requiring the signal to be converted or isolated. This article taps in USB applications in industrial environments and answers why it continues to be the I/O protocol of choice for many demanding industrial and edge-based computing projects. It should help you answer common questions like below when selecting, converting, isolating or expanding USB protocol for integration with your embedded systems.
- What bus is recommended for the data bandwidth required by my application?
- Is power available for charging or powering my connected device?
- Will anything interfere with my signals, or should I need to isolate?
- Can USB endure my rugged application? It is a harsh environment prone to failures.
- Do I need to upgrade legacy devices?
Industrial USB Hubs, Isolators, Converters, Expansion Cards
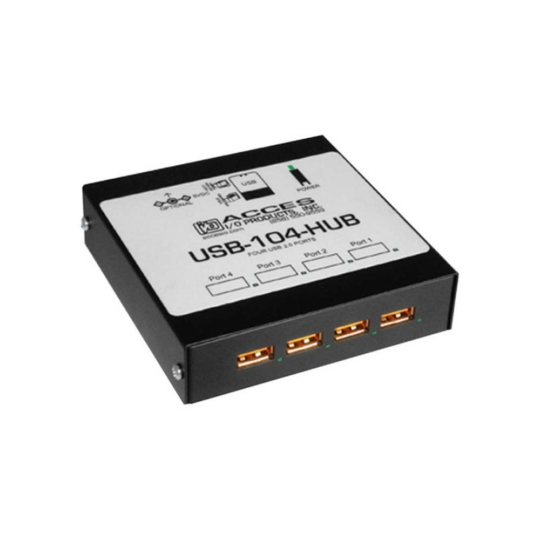
Industrial USB Hubs
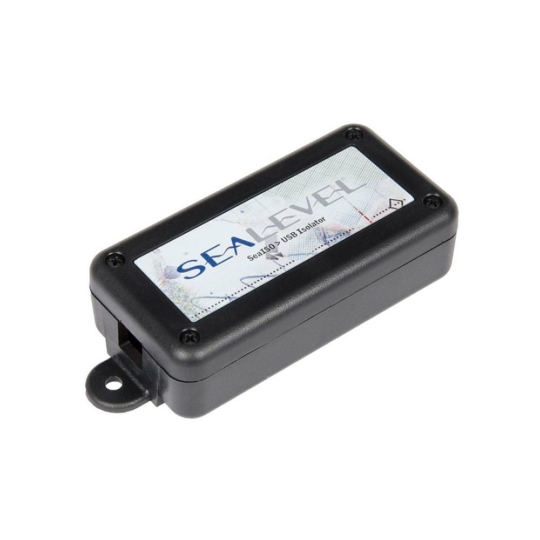
USB Isolators
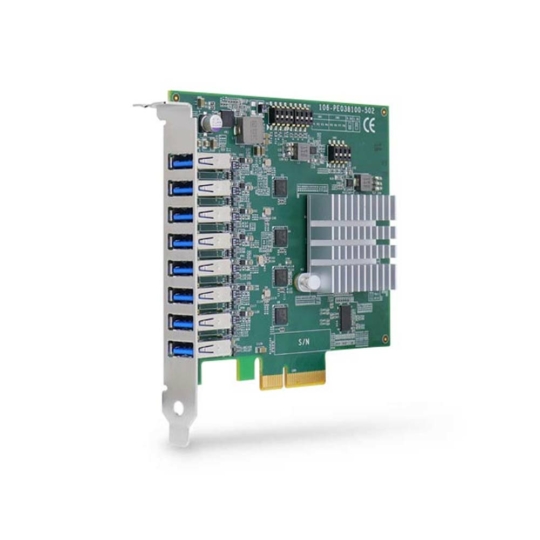
USB Expansion Cards
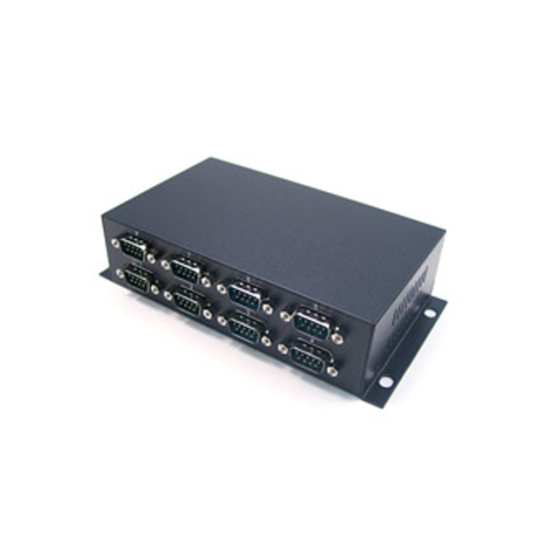
USB to Serial Converters
Embedded and Industrial USB Applications
Industrial Automation: Industrial PCs with large channel counts of USB can also be used to control equipment, automate systems and used in industrial testing environments. Due to increase channel count requirements in industrial automation, addition channel breakout can be achieved via an industrial USB 3.0 hub. They are programmed, controlled and changed to meet specific testing, automation, power delivery and data transfer needs. Typically deployed in localized cabinets to the data source, these systems operate under intense conditions that may be utilized during testing. Both power and data are transferred from cameras and sensors to help make predictions and actionable commands in both robotic automation and improved infrastructure on production line. Latest USB generations supporting high bandwidths are pushing boundaries for Smart Automation as part of Industry 4.0.
Kiosk and Vending Machine Peripheral Device Management: OEMs depend on board level solutions for integrating inside their kiosks and vending machines. USB is the ideal protocol for localized I/O and can be easily integrated to communicate with peripheral devices such as card readers, printers, NFC/RFID sensors, keypads, and more. Industrial motherboards and single board computers are commonly used with larger form factors capable of hosting higher channel counts of USB. Additional board level connectors are typically available for both USB 2 via 2.54 pitch headers and USB 3 via a 20-pin connector.
Security and Smart City Surveillance: In order to monitor city activity, surveillance computers usually require the latest generation USB standards to connect and communicate with different cameras and sensors throughout the city. The high-speed full-duplex data transfer capabilities makes USB an ideal protocol option for security and smart surveillance. To fulfil all indoor and outdoor security requirements, both surveillance PC and/or rugged USB hub must be able to withstand inclement weather.
Medical: Medical OEMs who want to take advantage of USB’s plug-n-play convenience, hot swappable capabilities and robust peripheral support must often factor in isolation for safety concerns. The IEC60601 medical standard requires isolation between all interfaces and peripherals particularly those at patient points of contact. 4kV isolation is therefore a standard requirement.
In-Vehicle, Military and Unmanned Systems: Battlefield conditions and deployment on moving vehicles, particularly unmanned systems at high altitude, must withstand shock, vibration, and extreme temperature swings. Latching USB or circular locking M12 USB connectors are a must have when deploying USB protocol for communication in moving vehicles to provide a reliable and rugged connection between devices. Typical devices to connect via USB in Military applications include sensors such as GPS, vision cameras, portable handhelds and battlefield equipment such night vision goggles. High-speed charging is a must have requirement for these kinds of devices and can be achieved with high channel count rugged USB hubs. High bandwidths are also required for deploying vision cameras, allowing the embedded systems to access the data quickly for processing with artificial intelligence.
Advantages of USB in Industrial Applications
Availability in M12 Locking or Latching USB Connectors: Rugged computers are available with M12 USB connectors and latching type A USB connectors. The ability to screw this connector down increases the systems level of endurance in harsh environments where shock and vibration can easily disconnect a standard connector.
Ability to Power Devices: A key advantage of USB is the ability to power connected devices without requiring an additional power source or supply in place. This reduces the requirement for cable management and can not only simplify installation and increase levels of portability but also reduce hidden costs.
Backwards Compatibility: Providing the right connector type is used, all legacy versions of USB can be used with the newest and latest generations on the market. This backwards compatibility which USB offer means that users do not have to worry about which generation of USB their device or host PC supports. This achieves a lower cost of ownership when introducing new technologies as legacy devices can still be used without the need to upgrade unnecessarily.
Hot-swappable Capabilities: Hot-swappable capabilities are crucially important in industrial applications. Hot-swappable USB enables industries to replace, and upgrade installed devices such as sensors without having to shut down and reboot a control system or edge computer. It is not recommended to remove devices which are transferring critical data such as data storage devices.
Expansion via Industrial USB Hubs: In use cases where you have reached max capacity and used up all available USB ports on your IIoT Gateway the option to expand via a USB hub designed for industrial use is an option. It is recommended to decide what is to be connected via the hub as the speed to uplink all connected devices will be limited by the host. As more IoT devices are connected the data transfer rate can decrease, meaning an industrial USB 3 hub will have greater capabilities than an industrial USB 2 hub.
Industrial USB Connectors: Locking, Latching and Circular M12
USB connectors found on embedded computing and I/O devices come in two different types: standard and industrial. Standard USB connectors are the most common type and can be found on everything from vision cameras to sensors. The proven designs such as Type A, B and Type C are small, lightweight, and easy to use. For most use cases where ingress protection or endurance against shock and vibration isn’t required, a standard USB connector is suitable for many applications.
Industrial USB connectors, on the other hand, are designed for more rugged applications. Both industrial and military users have a high demand for USB connections that provide complete reliability, dependability, and remain free from any failure. The industrial USB connectors are larger than standard connectors to provide locking or latching connectivity. Rugged PCs can often be found utilising standard USB connectors with optional locking screw connectors for connectivity with industrial USB cables. Industrial Hubs utilize similar designs which provide latching connectors for both Type A and Type B connector types. Both of these Type A and Type B USB connections provide the foundation on many industrial-grade USB Hubs with a design change which provides a high retention, locking design that complies with the class 1 Div II minimum withdrawal requirement. These connectors are designed with a positive lock tab to quickly differentiate them from standard USB ports and can withstand over 11 pounds of force to separate the latching connector. M12 USB connectors are another industry standard which not only provide security against shock and vibration but have a strong outer shell that is resistant to damage and ingress from dust, water, and impact. Industrial USB connectors are also typically rated for a higher number of insertions and withdrawals, making them ideal for applications where the connector will be frequently connected and disconnected.
Development of USB Technology Since 1996
USB 1.0 / 1.1
The original USB 1.0 standard was introduced in 1996, with a maximum speed of 12 Mbps. USB 1.0 was designed to connect 2 simple devices such as mouse and keyboard together on one computer. The development of USB was a long and arduous process as the first version did not allow for extension cables and power delivery making it difficult to gain a foot holding in the market. USB 1.1 was later introduced into the market to deliver on these requirements and from here USB initiated its universal adoption in the market. Both USB 1.0 and USB 1.1 were compatible with USB Type A and Type B connector types. Maximum cable length for communication with the original USB standard was 3M.
USB 2.0 (High-Speed USB, High Bandwidth Bus)
With continued growth as the universal standard for connecting devices, engineers were encouraged to continue developing the protocol for further reliability and even fast bandwidth. USB 2.0 was released in April 2000 setting a new standard in transfer rates and achieving speeds up to 480 Mbps. This was a significant upgrade being able to transfer data between the device and host PC up to 40 times faster.
Maintaining compatibility with the previous USB 1.0/1.1 generations was key. Making the new high-speed USB backwards compatible allowed users to connect their previous generation USB devices with the new high bandwidth bus found on modern day computers of its era. Not only did USB 2.0 succeed in replacing the first generation of USB with its more reliable data transfer speed, but it also offered a power delivery of 2.5W, 5V, and a maximum of 500mA current.
A host of new connector types became available for USB 2.0, the common standards continued to be USB Type A and USB Type B but there was also an addition of mini and micro connectors, including: Mini A, Mini B, Mini AB, Micro A, Micro B, and Micro AB. Supported cable length for USB 2 was also increase from 3M to 5M.
USB 3.2 Gen 1 (USB 3.0, USB 3.1 Gen 1) – SuperSpeed USB 5Gbps
With continued advancement in connected technology such as the mass adoption of IoT devices, especially IIoT devices in industrial applications, there was a big uptake in demand for higher bandwidths and an increased number of ports to connect these devices. The introduction of USB 3.2 Gen 1 in 2008 enabled more reliability and smoother data transfer speeds. Also known as the SuperSpeed USB 5Gbps, USB 3.2 Gen 1 offers much greater bandwidths than USB 2.0 and supports up to 5Gbps of data transfer speed.
The latest USB 3.2 versions also introduced a new full-duplex mode that allows two devices to transfer and receive data at the same time simultaneously. Full duplex is also backward compatible with previous versions of USB, making it a convenient upgrade for existing industrial systems requiring a boost in data transfer speeds.
Type A and Type B USB connectors continued to dominate but Micro B SuperSpeed connectors were also used. The max cable length supported was back down to 3M in length.
USB 3.2 Gen 2 (USB 3.1, USB 3.1 Gen 2) – SuperSpeed USB 10Gbps
Formerly known as the USB 3.1, USB 3.2 Gen 2 doubled the provided bandwidth and offered a new Type C USB connector type. USB 3.2 Gen 2 often goes by the name of “SuperSpeed USB 10 Gbps”, so you can keep track of which cables and ports are compatible with this new standard. With USB 3.2, you can transfer files at twice the speed of before which is important for vision-based applications when transferring high quality uncompressed video for inference. The adoption of USB Power Delivery also allowed for a potential 100 watts through supported PoE enabled hardware.
USB 3.2 Gen 2×2 (USB 3.2) – SuperSpeed USB 20Gbps
Released in August 2017 USB 3.2 was a significant update to transfer speeds in embedded applications with its compatibility made on the new USB Type-C connector. USB 3.2 provided the fastest data transfer speed available, with up to 20 Gbps of capability. Industrial grade Type C USB connectors are now being released to include this latest standard for premium bandwidth in industrial applications. The maximum cable length support USB 3.2 Gen 2×2 remains at 3M.
USB4
Since its launch in 2019, the USB4 standard continues to show significant increases in data transfer speeds with up to 40Gbps bandwidth. This comes at a cost though and maximum cable length is as short as 0.8 meters. In addition to only adopting Type-C connectivity, many industrial applications cannot support USB4. The previous USB versions are preferred and still widely used for current industrial applications however it can be suitable for OEM embedded applications not subject to harsh environments.
Why Isolate Your USB Signals? Avoid Damaging Surges and Transients
There are a number of reasons why industrial and medical facilities might choose to isolate USB signals. First, industrial environments often involve harsh conditions that can damage sensitive electronic equipment. By isolating the USB signal, the connected equipment is protected from potential damage to the host control system. Additionally, industrial facilities often have a lot of electromagnetic interference (EMI). Isolating the USB signal helps to prevent this interference from affecting the data being transmitted. Finally, industrial facilities often have a lot of power supplies with different voltages. Isolating the USB signal helps to ensure that the data is not corrupted by these different voltages. In short, there are a number of good reasons why industrial facilities might choose to isolate USB signals. USB isolators can provide up to 4 kV of protection, which is essential in environments where there is a risk of electrical shocks or surges. Industrial USB hubs also available often have built-in isolation filters that help to protect sensitive equipment from damage. By isolating the USB signal, you can help to ensure that your devices will function properly and communicate effectively.
Connecting Legacy Serial Devices to USB with Signal Converters
Serial ports are a simple and reliable way to connect one device with another. They’re great for low-speed data transport being capable of reliably transmitting individual bits of information at a time. Industrial PCs with high channel counts of serial ports are often used in factory environments to connect to things such as sensors and industrial control equipment because they offer this simple and reliable communication of data. The use of a single serial port for communication between sensing, monitoring and control devices is an excellent way to ensure that all systems are working in concert. For this reason, industrial automation systems have utilized serial communication for decades to network, monitor and control industrial processes. A big advantage of serial over USB is simple integration without the requirement for custom drivers to be installed on the host IPC as most operating systems provide native support for interfacing with serial devices.
That being said, serial devices can be connected to computers that do not have a serial port. A USB to Serial converter is a simple way for your computer and other devices that don’t have serial ports or want an easy connection. When a USB to Serial adapter has been plugged into your industrial computer, an individual COM port will be available for communicating with serial devices. This can save unnecessary costs to change out or replace legacy sensors and devices connected to date industrial controllers when implementing industry 4.0 and making automation within your facility smarter.
Need Help Expanding, Isolating, or Converting USB Signals?
Tell us about your application and a member of our team will get right back to you.