Synchronizing Machine Vision with Precision: IEEE-1588 PTP
Machine vision systems often require high precision synchronization of cameras and other sensors to accurately capture and process visual data. This is where IEEE 1588 Precision Time Protocol (PTP) comes in and is often integrated into our range of Edge AI Computers, or is enabled on one of our rugged ethernet switches.
IEEE 1588 PTP is a protocol used to synchronize clocks in a network to sub-microsecond accuracy. By using PTP, the clocks of multiple devices in a machine vision system can be synchronized to a common time reference, allowing them to work together seamlessly and accurately.
In a machine vision system, PTP can be used to synchronize the triggering of cameras and other sensors, ensuring that they all capture images at precisely the same moment. This is important for applications where multiple cameras are used to capture a scene from different angles, as well as for applications where multiple sensors are used to capture different types of data, such as color and depth information.
PTP is also useful for applications where real-time processing of visual data is required, such as in robotics and autonomous vehicles. By ensuring that all devices in a system are synchronized to the same clock, PTP can help reduce latency and improve the accuracy of visual data processing, allowing for more precise and efficient operation of these systems.
Machine Vision Control Systems and Network Cards for IIoT
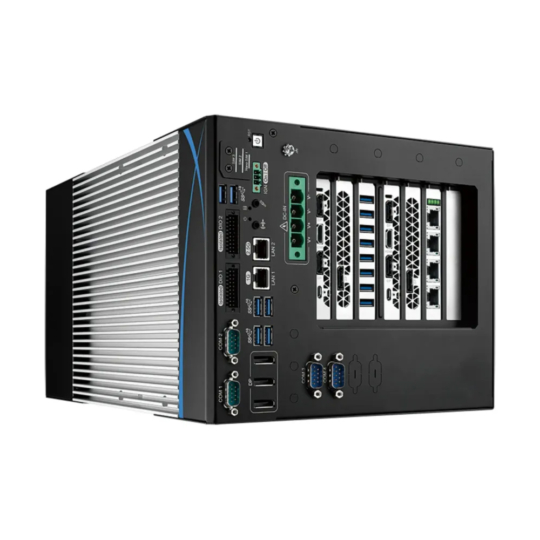
Machine Vision Training Servers
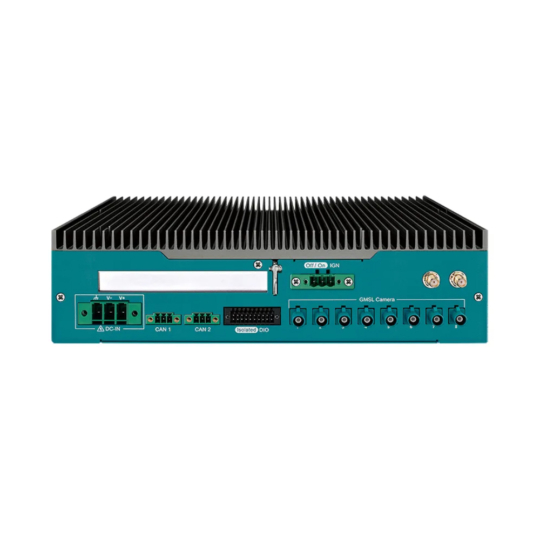
Edge AI Inference PCs
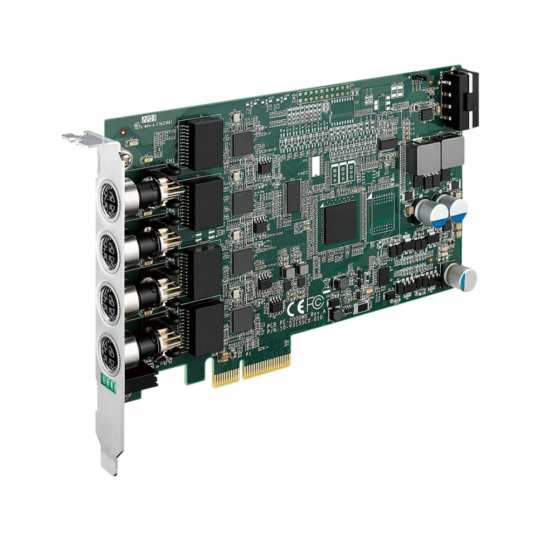
PCIe LAN Cards with PTP
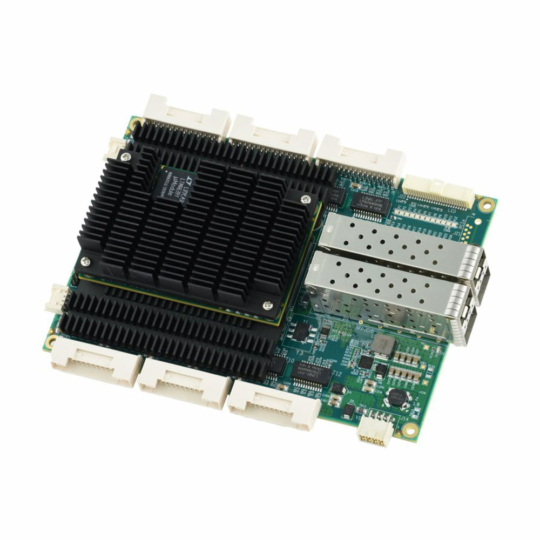
Rugged Ethernet Switches
Examples of Machine Vision Among Different Industries
Machine vision refers to the ability of machines, such as computers and robots, to interpret and understand visual information. Some examples of machine vision applications include:
Quality control: Machine vision is commonly used in manufacturing to ensure that products meet certain quality standards. For example, machine vision can be used to inspect components for defects or to ensure that packaging is properly sealed.
Autonomous vehicles: Self-driving cars and other autonomous vehicles rely on machine vision to detect obstacles and navigate roads. Cameras and other sensors are used to gather visual information about the vehicle’s surroundings.
Medical imaging: Machine vision is used in medical imaging to help doctors diagnose and treat a variety of conditions. For example, machine vision can be used to analyze X-rays, CT scans, and other medical images to help doctors detect tumors, fractures, and other abnormalities.
Security and surveillance: Machine vision can be used in security and surveillance applications to monitor public areas and detect potential threats. For example, cameras can be used to track individuals or vehicles and alert security personnel if they behave in suspicious ways.
Agriculture: Machine vision can be used in agriculture to monitor crops and improve yields. For example, cameras can be used to detect plant diseases or to monitor the growth of crops over time.
Robotics: Machine vision can be used to help robots navigate and interact with their environments. For example, robots can use machine vision to detect and grasp objects, or to navigate around obstacles.
What is the IEEE-1588 Precision Time Protocol (PTP)?
The IEEE-1588 Precision Time Protocol (PTP) is a protocol used for time synchronization in computer networks. It is designed to achieve sub-microsecond accuracy for time synchronization between clocks in a distributed network.
The PTP protocol works by establishing a master-slave relationship between clocks in the network. The master clock sends periodic timing messages to the slave clocks, which use the information in these messages to adjust their own clocks to be in sync with the master clock.
PTP has several features that make it useful for time synchronization in applications such as industrial automation, telecommunications, and audio/video production. These features include:
High accuracy: PTP can achieve synchronization accuracy of sub-microseconds, which is essential for applications that require precise timing.
Dynamic adjustment: PTP allows clocks to be adjusted dynamically to compensate for changes in network delay or other factors that can affect synchronization accuracy.
Fault tolerance: PTP supports redundant master clocks and failover mechanisms to ensure that time synchronization can continue even in the event of a failure.
Scalability: PTP can be used in networks of any size, from a few devices to large distributed systems with thousands of devices.
Overall, the IEEE-1588 Precision Time Protocol (PTP) is a powerful tool for achieving accurate and reliable time synchronization in distributed networks.
How Does IEEE-1588 PTP Benefit Machine Vision Applications?
The IEEE-1588 Precision Time Protocol (PTP) is particularly beneficial for machine vision applications because it provides highly accurate time synchronization for cameras and other sensors. Here are some of the main benefits of PTP for machine vision:
Accurate synchronization: PTP allows cameras and other sensors to be synchronized to a common time reference with sub-microsecond accuracy. This is essential for applications such as 3D imaging, where multiple cameras need to capture images of a scene simultaneously.
Reduced latency: PTP can help reduce the latency between cameras and other sensors in a machine vision system, which can improve the accuracy of visual data processing.
Improved reliability: By ensuring that all devices in a machine vision system are synchronized to the same clock, PTP can help reduce errors and improve the overall reliability of the system.
Flexibility: PTP can be used in a wide range of machine vision applications, from quality control and inspection to robotics and autonomous vehicles.
Scalable: Networks of any size can implement PTP, making it suitable for machine vision systems of all types, from small-scale applications to large distributed systems.
Overall, the IEEE-1588 Precision Time Protocol (PTP) is a powerful tool for improving the accuracy, reliability, and efficiency of machine vision systems. By providing highly accurate time synchronization for cameras and other sensors, PTP can help ensure that machine vision applications are able to capture and process visual data with maximum precision and efficiency.
How To Implement Precision Time Stamping To Industrial Networks
The availability of IEEE-1588 Precision Time Protocol (PTP) support on industrial PCs can vary depending on the specific hardware and software configuration. Some industrial PC manufacturers offer PTP support as a standard feature or as an optional add-on, while others may not support it at all.
When selecting an industrial PC for a machine vision or other time-sensitive application that requires PTP, it is important to check the product specifications to ensure that it supports the protocol. Additionally, it is important to ensure that the operating system and any software used in the application are also PTP-compatible.
If an industrial PC does not come with PTP support, it may be possible to add it using a PTP network card or other PTP-enabled hardware. However, it is important to ensure that any additional hardware is compatible with the industrial PC and the application requirements.
Here are the basic steps involved in implementing PTP:
Install PTP hardware: PTP requires hardware components that support the protocol, including PTP-capable network interface cards (NICs) and switches. These components are typically available from vendors that specialize in PTP hardware.
Configure PTP software: PTP software is required to manage the protocol and synchronize the clocks in a network. This software is typically provided by the hardware vendor or is available as open-source software.
Connect PTP-enabled devices: Connect the PTP-enabled devices, such as cameras and sensors, to the PTP-enabled network. This can be done using standard Ethernet cabling.
Configure PTP settings: Configure the PTP settings on each device, including the master/slave configuration and the synchronization interval.
Test and verify synchronization: Once the PTP settings have been configured, test and verify that the clocks in the network are properly synchronized. This can be done using PTP measurement tools, which are available from hardware vendors and open-source software projects.
Monitor and maintain the PTP implementation: Monitor the PTP implementation over time to ensure that synchronization remains accurate and reliable. Make any necessary adjustments to PTP settings as needed.
Overall, implementing the IEEE-1588 Precision Time Protocol (PTP) requires careful planning and coordination between hardware and software components. However, the benefits of PTP, including highly accurate time synchronization and reduced latency, make it an essential tool for machine vision and other applications that require precise timing and synchronization.
Looking For An IEEE-1588 Enabled Industrial PC or Network Card?
Tell us about your application and a member of our team will get right back to you.