What is Optical Bonding? Benefits and Use Cases in Industrial Environments
If you’re suffering from poor visibility when viewing your embedded or industrial display outdoors then optical bonding could solve your problem. In almost all TFT LCDs there is an air gap between the TFT panel and the cover lens, this is known as air bonding. Having an air gap causes a multitude of problems in harsh industrial or outdoor environments including condensation build-up and poor visibility from glare. Applying a layer of resin and filling this air gap can bring numerous benefits later discussed in this article.
Things Embedded have supplied optically bonded screens across various industries, including the military, marine, medical, transportation, and retail sectors. These sectors often require a display or panel PC that can withstand harsh environments and deliver superior performance in outdoor, high bright, and damp conditions. Partnering with global leaders in design and manufacture of embedded and industrial LCD displays and touchscreens, we can offer optical bonding services as needed. If you require an optically bonded display or an optically bonded panel PC, please reach out.
What is Optical Bonding?
Optical bonding is a highly specialized process used in the manufacturing of monitors and displays. It involves the application of a layer of resin, known as an optical bonding adhesive, between the glass or touchscreen and the TFT LCD panel of the monitor.
The purpose of optical bonding is to eliminate any gaps or pockets of air that may exist between the different layers of the monitor. These gaps can cause several issues, such as reduced visibility, decreased touch sensitivity, and increased susceptibility to moisture and dust. By bonding the layers together, the optical bonding process ensures a seamless and more rugged display.
The resin used in optical bonding is typically optically clear and has excellent adhesive properties. It is carefully applied to the surface of the TFT LCD panel, ensuring complete coverage and uniform thickness. The glass or touchscreen is then carefully placed on top of the resin layer, and pressure is applied to ensure a strong bond.
Advantages Of An Optically Bonded Screen
Optically bonded displays offer numerous advantages by eliminating the air gap between the display panel and cover glass through the use of optical adhesive. This results in enhanced visibility with reduced glare and reflections, making them ideal for outdoor and well-lit environments. The durability of these displays is improved as they are less susceptible to moisture, dust, and damage, ensuring long-term performance. Touch accuracy is heightened due to minimized parallax and closer proximity of touch sensors, while the absence of an air gap also facilitates better heat dissipation, contributing to their thermal efficiency. Additionally, these displays exhibit superior color vibrancy, contrast, and water/dust resistance, making them well-suited for demanding applications like outdoor signage, industrial controls, and medical devices.
Optical Bonding Prevents Condensation
One of the main advantages of optical bonding is its ability to prevent condensation from forming on the screen. Condensation occurs when there is a significant difference in temperature between the environment and the display module. In traditional displays, the air gap between the panel and the protective glass can create a space for moisture to accumulate, leading to foggy or blurred visuals. However, with optical bonding, this issue is effectively addressed as the adhesive fills the gap, leaving no room for condensation to occur.
This feature makes optical bonding particularly beneficial for outdoor applications where consistent temperatures cannot be maintained. In such environments, where the display module is exposed to varying weather conditions, the risk of fogging or condensation is high. However, with optical bonding, the display remains clear and unaffected by these external factors, ensuring optimal visibility and performance.
Furthermore, the prevention of dust and liquid ingress is another significant advantage of optical bonding. Dust particles and liquid droplets can easily find their way into the display module through small gaps or openings. Once inside, they can cause damage to the internal components, affect the display quality, or even lead to malfunctioning. However, with the elimination of the air gap through optical bonding, the risk of dust and liquid ingress is greatly reduced, ensuring the longevity and reliability of the display.
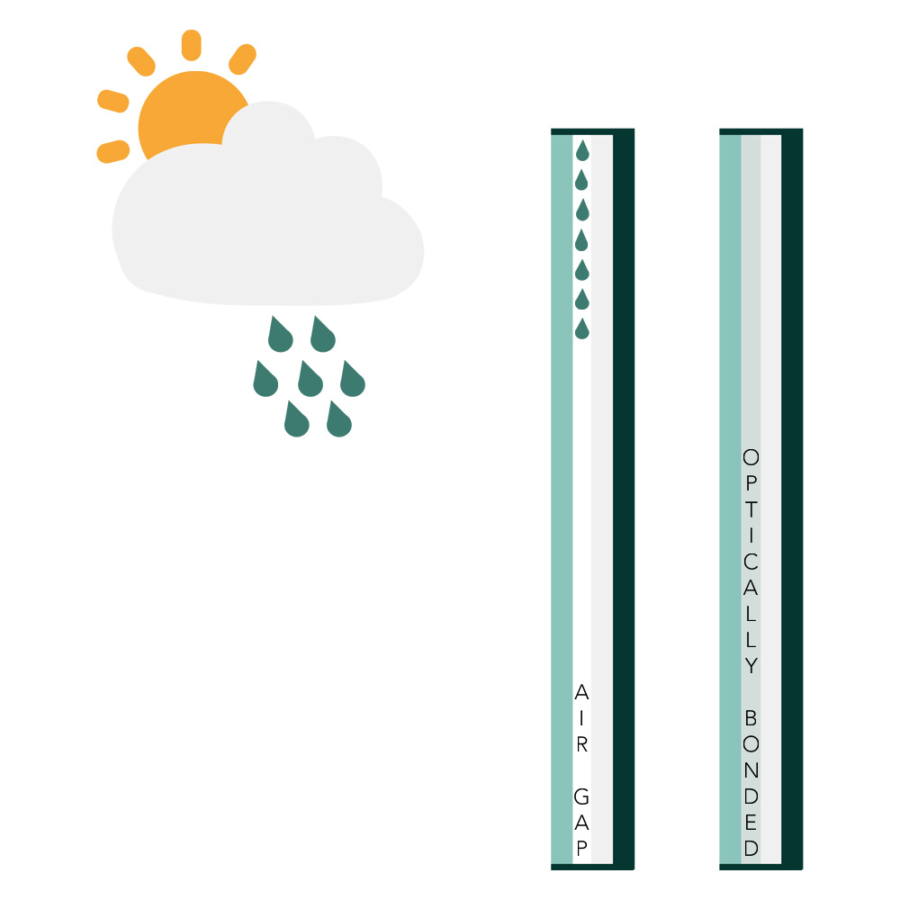
Optical Bonding Increases Durability
The additional resin layer in optical bonding refers to a process where a layer of resin is applied between the display panel and the cover glass of a device. This resin layer serves multiple purposes, one of which is absorbing shock. When a device with optical bonding is subjected to impact or vibration, the resin layer acts as a cushion, absorbing the force and preventing it from directly affecting the display panel.
By absorbing shock, the resin layer significantly enhances the durability of the screen. It reduces the risk of damage that can occur from accidental drops, bumps, or other physical impacts. This is particularly important in public access areas, where devices are often handled by multiple users and are more susceptible to accidental mishandling. The resin layer helps to protect the screen from cracking, shattering, or other forms of damage that can render the device inoperable.
Moreover, the presence of the resin layer also makes the screen less prone to damage from vandalism. In public spaces or areas with a higher risk of intentional damage, such as factories or harsh environments, the screen of a device can be a target for vandalism. However, the additional resin layer acts as a barrier, making it more difficult for vandals to scratch, etch, or deface the screen. This helps to maintain the integrity and functionality of the device, even in environments where it may be subjected to intentional acts of damage.
Overall, the inclusion of an additional resin layer in optical bonding provides high durability for devices used in public access areas, factories, or other harsh environments. It offers protection against accidental impacts and vandalism, ensuring that the screen remains intact and functional even in challenging conditions. This makes optical bonding an ideal choice for applications where durability and resilience are paramount.
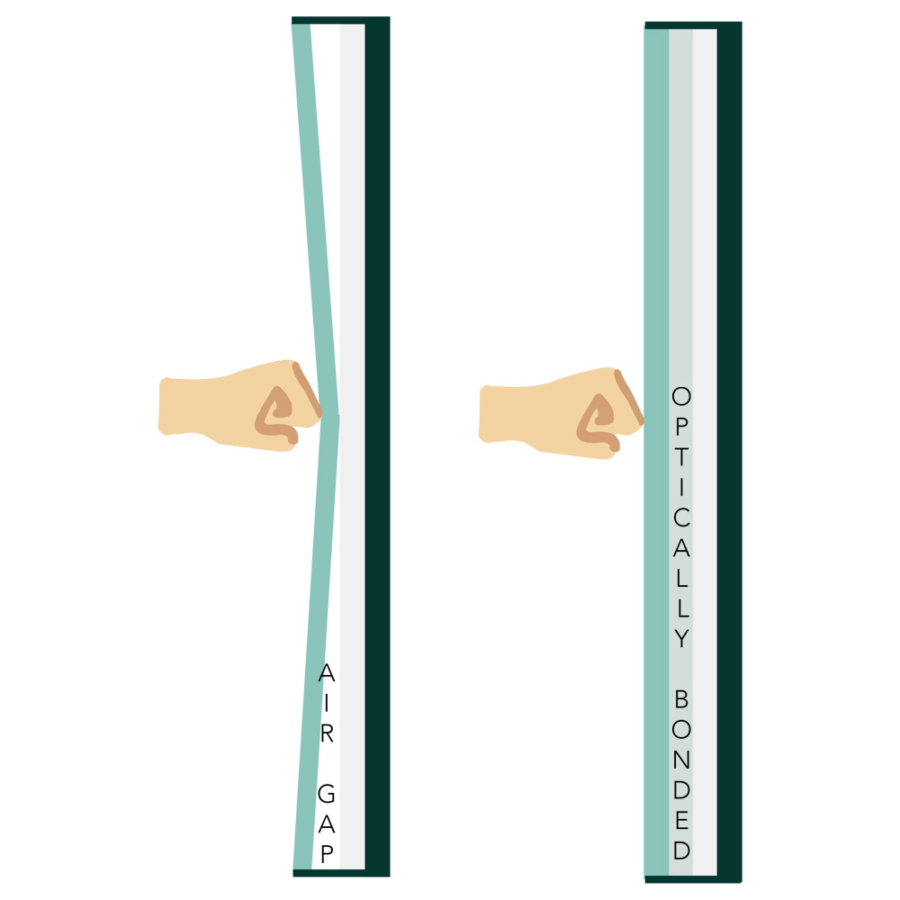
Optical Bonding Reduces Glare
When light hits a non-bonded screen, it encounters an air gap between the glass and LCD module. This gap creates opportunities for refraction, which refers to the bending of light as it passes through different mediums. As a result of refraction, external light that hits the screen is bounced back off the screen towards the viewer. This bouncing of light creates glare, which can be quite bothersome and hinder the visibility of the screen.
On the other hand, when the glass and LCD module are bonded together, the light passes through the bonded layers without encountering any gaps. As a result, the light is not subjected to significant refraction and is able to pass through the screen more smoothly. However, it is important to note that even when the layers are bonded, some amount of light is still absorbed by the screen. This absorption occurs as the light interacts with the materials present in the screen, such as the LCD panel and other components.
Overall, the bonding of the glass and LCD module in a screen helps to reduce glare by minimizing the opportunities for refraction. However, some amount of light absorption still occurs, which can affect the overall brightness and clarity of the displayed content.
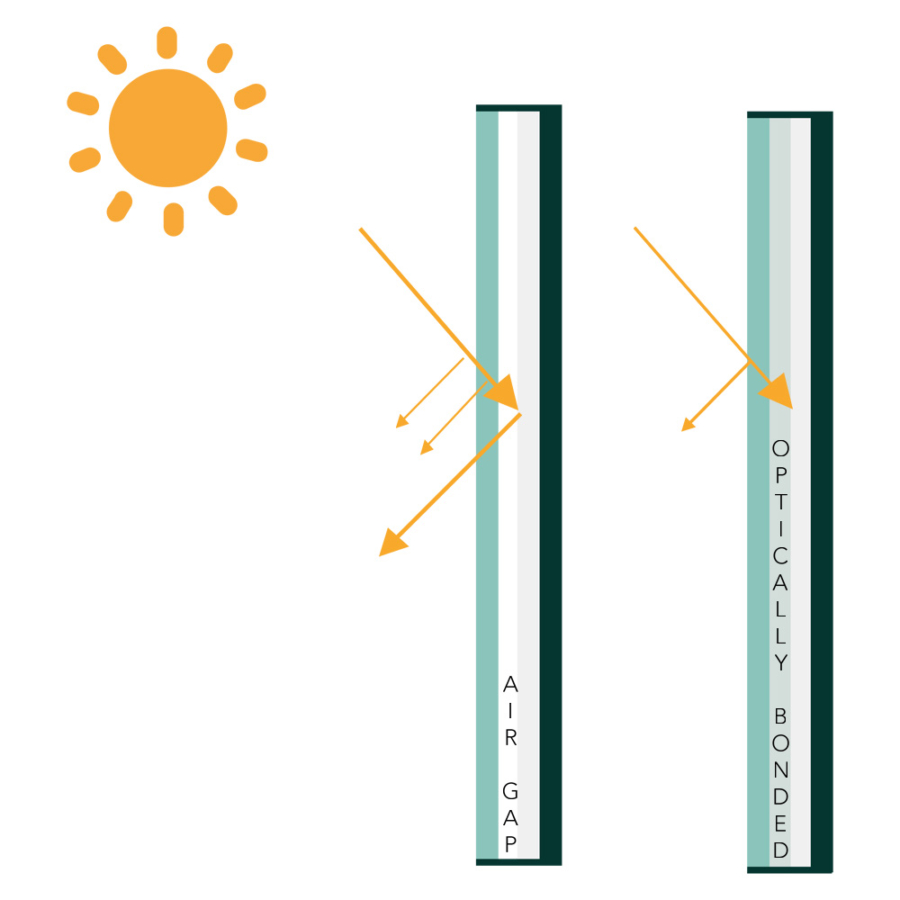
Touch Screen Optical Bonding Improves Accuracy
A touch monitor with optical bonding refers to a display technology where a layer of adhesive material is used to bond the touch panel directly to the display panel. This process eliminates the air gap that typically exists between the two panels in traditional touch monitors.
By eliminating the air gap, optical bonding touch screen components ensures that the touch response is more accurate and precise. When a user touches the screen, the pressure applied is immediately transmitted through the substrate, which is the material that makes up the display panel. This direct transmission of pressure allows for a faster and more immediate response from the touch panel.
In contrast, traditional touch monitors with an air gap between the touch panel and the display panel may experience a slight delay in touch response. This delay occurs because the pressure applied by the user's touch needs to travel through the air gap before reaching the touch panel. The air gap can introduce a small amount of resistance and hinder the immediate transmission of pressure.
The absence of an air gap in an optically bonded touch monitor ensures that the touch response is not delayed or hindered by any resistance caused by the gap. This results in a more accurate and responsive touch experience for the user.
Overall, a touch monitor with optical bonding provides a superior touch experience by maintaining a more accurate touch response through the direct transmission of pressure, eliminating any delay caused by an air gap.
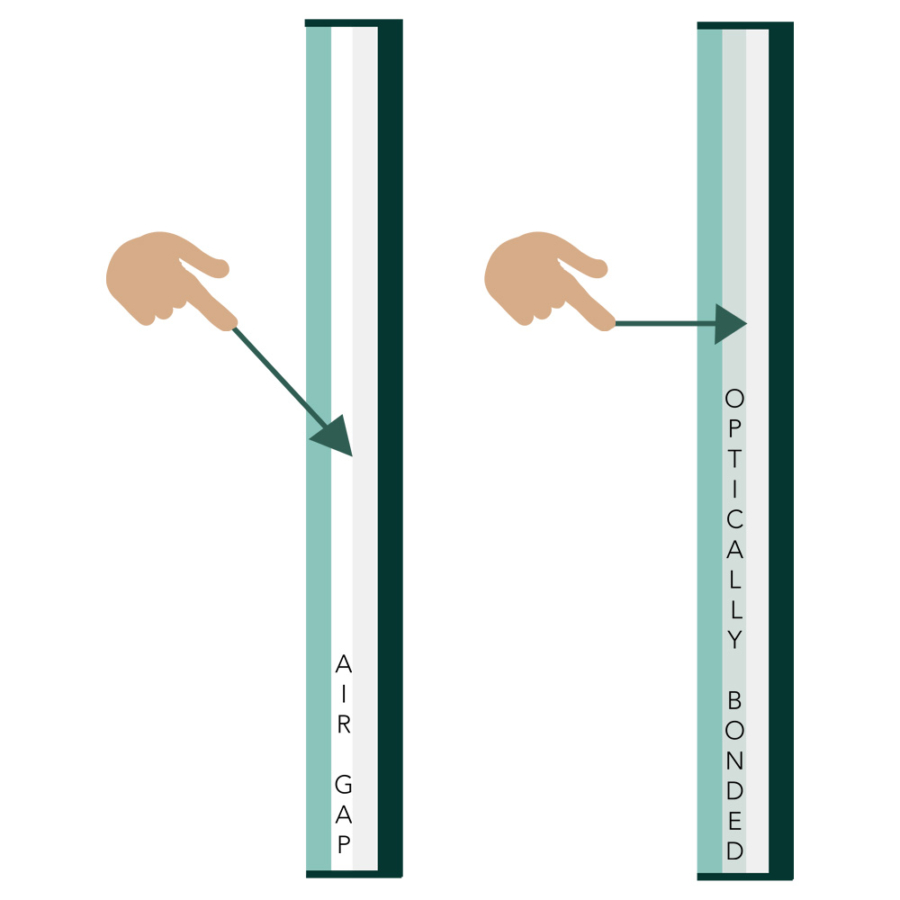
Dry Optical Bonding vs Liquid Optical Bonding
Dry optical bonding and liquid optical bonding are two different methods used to enhance the performance and durability of displays. Both techniques aim to reduce the reflection and increase the contrast of the display, resulting in improved visibility and readability in various lighting conditions. Both dry optical bonding and liquid optical bonding are effective methods to enhance display performance and the choice between the two techniques depends on factors such as cost, application requirements, and desired level of optical performance and durability.
Liquid Optical Bonding
Liquid optical bonding is a process that involves the use of UV radiation to securely attach the touch panel directly to the LCD. This technique is commonly used in the manufacturing of electronic devices such as tablets and displays.
The process begins by applying a layer of optically clear adhesive (OCA) to the surface of the LCD. The OCA is a transparent material that helps to enhance the optical properties of the display, improving clarity and reducing reflections. The touch panel, which consists of a layer of glass or plastic with touch-sensitive sensors, is then carefully aligned and placed on top of the OCA.
Once the touch panel is in position, the assembly is exposed to UV radiation. The UV light activates a photochemical reaction in the OCA, causing it to cure and harden. This bonding process creates a strong and durable connection between the touch panel and the LCD, ensuring that they remain securely attached even under various environmental conditions.
Overall, liquid optical bonding is a highly effective and widely used technique in the industrial electronics industry. By securely attaching the touch panel directly to the LCD using UV radiation, this process improves touch accuracy, enhances visual quality, and increases the durability of screens in industrial settings.
Dry Optical Bonding
Dry optical bonding is a technique that involves using heat and pressure to securely attach the touch panel directly to the LCD. This process offers several advantages over other bonding methods.
One of the key benefits of dry optical bonding is its faster assembly process. By eliminating the need for adhesives or liquid materials, the bonding of the LCD and touch panel can be completed more quickly. This not only saves time during production but also allows for a more efficient manufacturing process overall.
The finished product achieved through dry optical bonding exhibits excellent resistance to shock and vibration. The direct attachment of the touch panel to the LCD ensures a strong and durable bond, making the device more robust and less susceptible to damage caused by external forces. This is particularly important for devices that are frequently subjected to rough handling or environments with high levels of vibration.
Dry optical bonding also helps to achieve a higher resonance frequency in the finished product. Resonance frequency refers to the natural frequency at which an object vibrates most efficiently. By securely bonding the touch panel to the LCD, any potential vibrations or oscillations are effectively dampened, resulting in a higher resonance frequency. This can lead to improved performance and enhanced user experience, especially in devices that rely on precise touch input or require high-speed response times.
In summary, dry optical bonding offers a faster assembly process, excellent resistance to shock and vibration, and a higher resonance frequency. These advantages make it a preferred bonding method for manufacturers looking to enhance the durability, performance, and overall quality of their LCD and touch panel devices.
Looking for an Industrial Optically Bonded Display?
Things Embedded are partnered with design and manufacturers for embedded and industrial displays with optical bonding service upon request.