NVIDIA Jetson Edge Computing Platforms Enable Safe Human-Robot Collaboration
In recent years, there has been a significant increase in the adoption of automation technologies in various industries, leading to the emergence of human-robot collaboration (HRC). This collaboration between humans and robots holds great promise for enhancing productivity, efficiency, and safety in the workplace. However, as this field continues to evolve, it is crucial to carefully assess and address the health and safety challenges associated with Cobots.
The benefits of Robots & Cobots are undeniable. By leveraging the strengths of both humans and robots, companies can achieve unprecedented levels of productivity and operational excellence. Robots can be programmed to perform repetitive, physically demanding, and dangerous tasks, however, this collaboration also introduces unique challenges that must be addressed to ensure the safety of nearby operators. One of the primary concerns in HRC is the risk of physical injury to human workers. The close proximity between humans and robots creates potential hazards, such as collisions, crushing, or entrapment incidents. Ensuring proper design and implementation of safety measures, such as barriers, sensors, and protective equipment, is crucial to mitigate these risks and prevent accidents.
GMSL (Gigabit Multimedia Serial Link) cameras have the potential to play a vital role in enhancing health and safety in the context of human-robot collaboration. These high-resolution cameras provide real-time visual feedback, enabling operators and robotic systems to have an accurate and detailed understanding of their surroundings. By deploying GMSL cameras strategically within HRC environments, potential hazards and risks can be detected promptly, allowing for immediate action to be taken. These cameras can capture and relay essential information, such as the location and movement of human workers, facilitating the implementation of safety measures and collision avoidance systems. With their advanced image processing capabilities and high-quality video output, GMSL cameras contribute to a safer Cobot ecosystem by enabling enhanced situational awareness, minimising the risk of accidents, and providing a reliable monitoring system for maintaining health and safety standards.
By deploying AI models directly on edge devices, such as the Robot’s embedded AI systems, real-time inference can be performed locally without relying on cloud connectivity. This enables rapid analysis of sensor data and immediate decision-making to address potential health and safety risks. Edge AI inference can power advanced algorithms for object detection, pose estimation, and gesture recognition, allowing robots to accurately perceive and respond to human presence and actions. For example, it can enable real-time detection of hazardous situations, such as a person entering a restricted area or a worker exhibiting signs of fatigue. By integrating edge AI inference with rugged GPU computers into HRC systems, safety measures and control mechanisms can be activated instantaneously, preventing accidents and ensuring the well-being of both humans and robots.
Latest Embedded AI Systems With GMSL Camera Capabilities
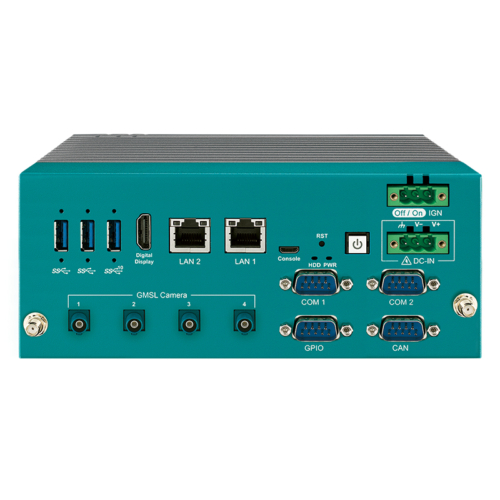
EAC-6100-R08
NVIDIA Orin NX Automotive Computer with 4x GMSL, CAN FD, and Ignition Sensing
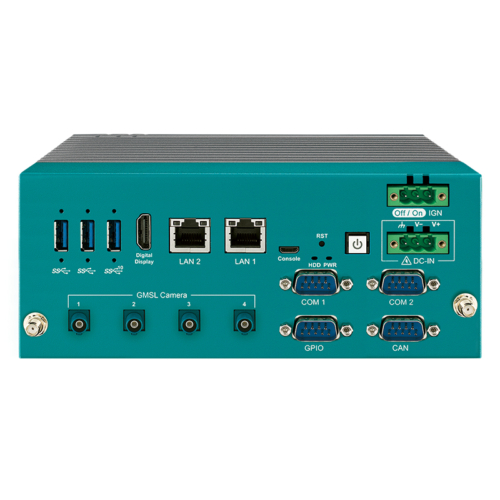
EAC-6100-R16
Jetson Orin NX In Vehicle Computer with 4x FAKRA GMSL, CAN FD, and Ignition Control

EAC-5000-R32
NVIDIA Jetson AGX Orin Low Profile Industrial PC with PCIe

EAC-5000-R64
NVIDIA Jetson AGX Orin Rugged GPU Computer with PCIe
Next-Gen Robotics Powered By NVIDIA Orin NX
Jetson Orin is a powerful and advanced AI computing platform developed by NVIDIA. It offers impressive AI inference capabilities, making it well-suited for various applications, including those related to health and safety in human-robot collaboration (HRC). The Jetson Orin NX incorporates a high-performance system-on-a-chip (SoC) with multiple processing units, including Arm Cortex-A78 cores, NVIDIA Ampere GPU, and dedicated AI accelerators.
The AI inference capabilities of Jetson Orin NX enable efficient and real-time analysis of sensor data in HRC environments. With its impressive compute power, the platform can handle complex deep learning models and algorithms, allowing for accurate object detection, pose estimation, and gesture recognition. This capability enables robots to perceive and understand human actions, ensuring enhanced safety in their collaboration with humans. Additionally, Jetson Orin NX supports a wide range of AI frameworks, libraries, and tools, providing developers with flexibility and ease of implementation. This enables the deployment of state-of-the-art AI models, such as deep neural networks, on the platform, enabling advanced decision-making capabilities. The platform also supports hardware acceleration for AI workloads, maximising inference performance while minimising latency.
The EAC-6100 robotics controller was chosen as the ideal rugged Jetson PC for enabling edge AI inference leveraging the Jetson Orin NX’s capabilities in conjunction with its GMSL camera capabilities. The EAC-6100 by Vecow offers seamless integration with either 8GB or 16GB Jetson Orin NX system-on-modules, providing a robust and reliable hardware foundation for deploying AI models and algorithms at the edge. With its powerful processing capabilities and optimised architecture, the EAC-6100 can efficiently handle the complex computations required for AI inference. Compatible with a wide range of GMSL cameras enhances the overall system’s perception capabilities, enabling high-resolution video input for accurate object detection, tracking, and safety monitoring. This next-generation of robotics controller allows human-robot collaboration to gain the advantage of real-time, local AI inference, further enhancing health and safety measures in collaborative environments.
Vecow’s latest robotics controller boasts several outstanding features that make it a top choice for industrial applications. First and foremost, its fanless operation ensures reliable performance and longevity by eliminating potential points of failure, such as dust accumulation or fan malfunctions. This design ensures seamless operation in harsh industrial environments, where the presence of debris or vibrations can affect the performance of traditional fan-based systems. Despite not having active cooling, the industrial-grade components integrated onboard Vecow’s EAC-6100 comfortably supports operation in the extreme temperatures found on factory floors.
Featuring onboard CAN bus, the EAC-6100 robotics controller enables seamless communication and integration with various industrial devices, such as sensors, actuators, and other control systems. This feature facilitates efficient and synchronised control of robotics automation processes, enhancing overall system performance and productivity.
Another notable feature of the EAC-6100 is its wide range 9-50V DC input with ignition sensing. This allows the controller to be powered by a diverse range of power sources, or fluctuating power sources, commonly found in industrial settings. The ignition sensing capability further enhances its suitability for use in vision computing applications, by enabling remote on/off functionality.
See How We Can Help With NVIDIA Jetson AI Computers
Tell us about your application and a member of our team will get right back to you.